Inxpect Safety
Radar Equipment
The next generation safety products
modern technology that offers superior safety
Inxpect safety products are made for advanced industrial automation and robotics systems based on radar technology. Our products can detect the entrance and presence of operators in dangerous areas and stop machinery from restarting until the area is free of people, also in the presence of dust, debris, smoke and dirt.
The system automatically switches between the 2 safety functions:
Access protection
System monitors the dangerous area:
- OSSDs are in ON-state
- Sensor sensitivity is low
- Static objects are automatically excluded
- Reaction time is 100ms
Area entered
Restart prevention
System scans the area for micro‑movements:
- OSSDs are in OFF-state
- Sensor sensitivity is high
- Static objects are automatically excluded
- System requires a restart timeout before switching back to access detection mode
Area cleared
Smart Safety
Industrial safety at its best: Inxpect safety radars detect access or presence of operators in dangerous areas, allowing real-time dynamic setting of the detection and warning zones.
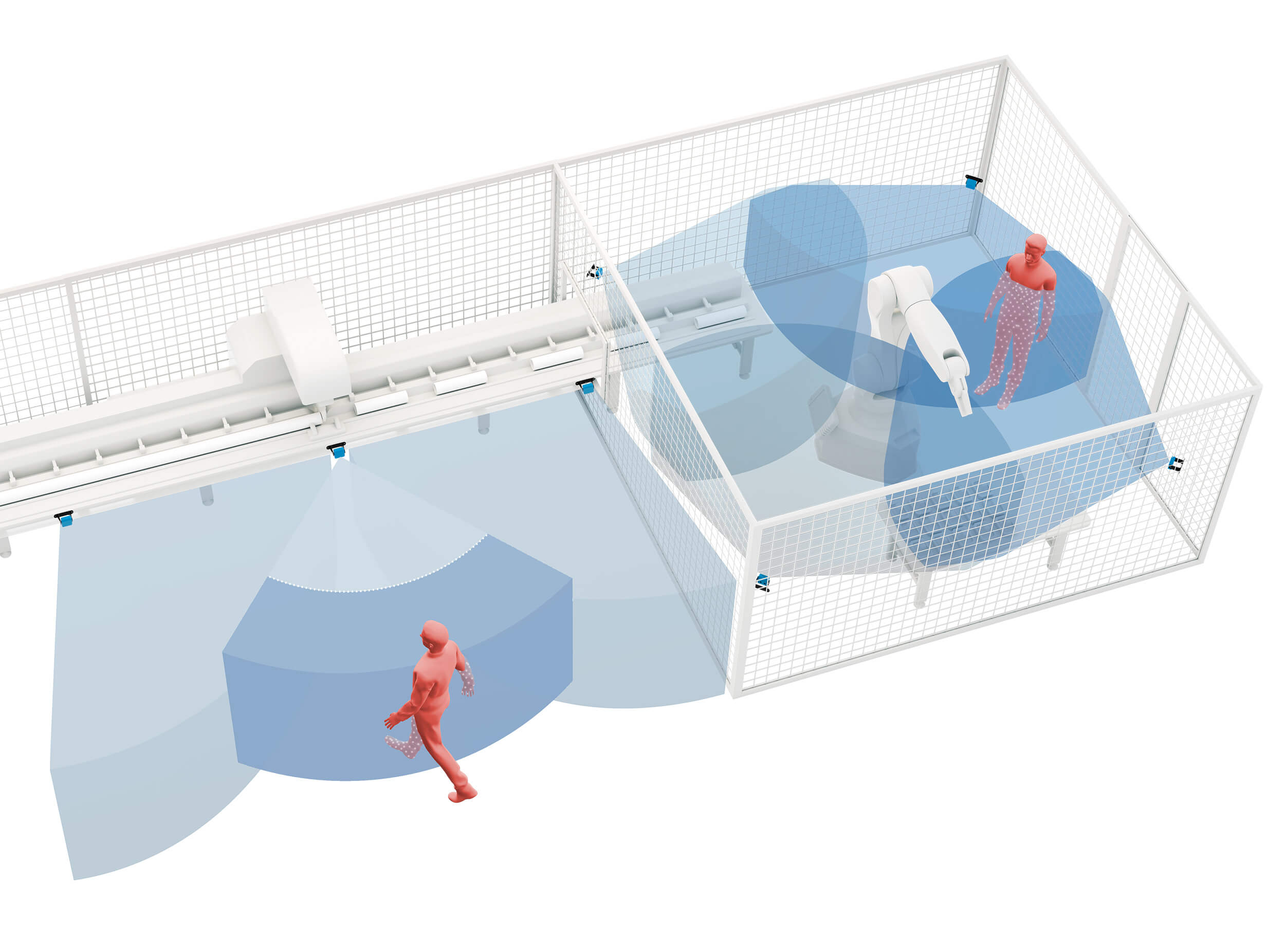
Inxpect Radar Sensors
World’s first and only SIL2/PLd and UL Listed safety radar products.
100 SERIES
200 SERIES
Pro Line
Plug & Safe Line
200 SERIES 9m
Pro Line 9m
Inxpect Control Units
The best interface to Inxpect safety radars for any type of machinery.
Type A
Type B
with SD card
Inxpect ruggedized Control Units
The most robust Inxpect Control Unit made for harsh environments.
Why choose Inxpect Safety Radar Equipment?
Inxpect Radar Sensors are resistant to any disturbances stemming from smoke, dust, shavings, sprays or machining residues.
The sensors can work at high sensitivity and can even detect the micro-movements of a person breathing to prevent accidental machine restart.
This radar intrinsically reads the space in 3D, providing volumetric coverage of the dangerous area.
Inxpect safety products are SIL2 certified, the most advanced safety level in the industrial sector.
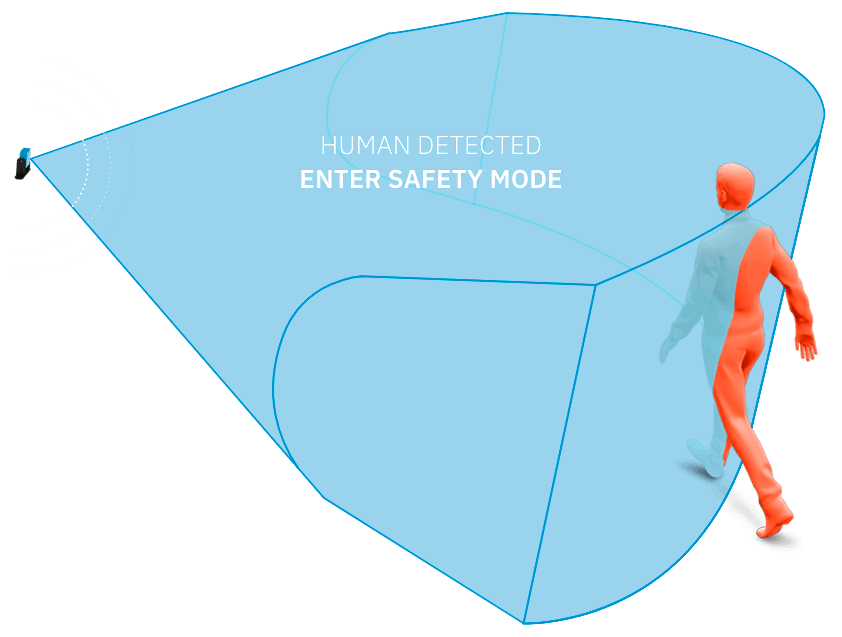
Nothing has ever been this safe
in the industrial sector
Inxpect safety products adapt to many different usage situations in a wide range of working environments. Below are some of the most common usage scenarios, where radar technology has significantly increased safety levels.
Want more information?